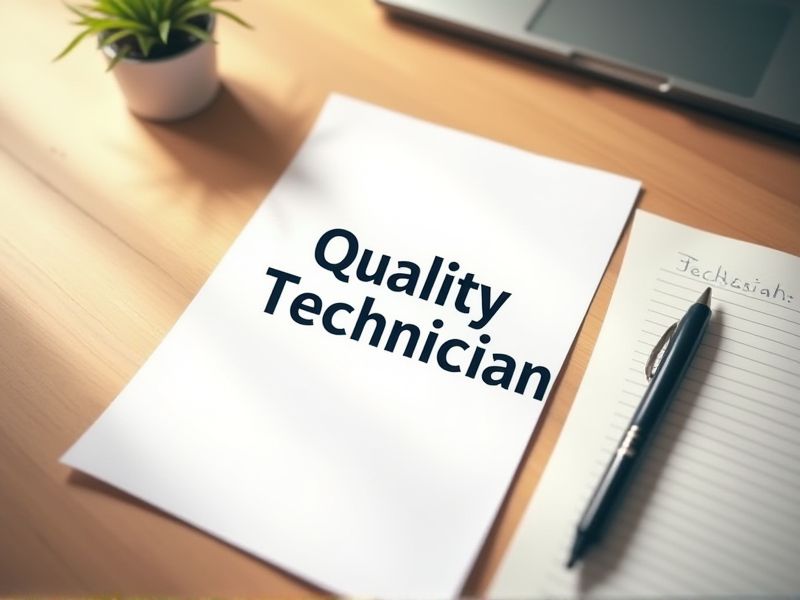
Quality Technicians play a crucial role in ensuring that products meet industry standards and customer expectations. Certifications validate their expertise and knowledge, thereby increasing trust and credibility in their skills. Achieving these certifications often signifies a commitment to quality, safety, and regulatory compliance. Here are some important certifications you may need to pursue a career as a Quality Technician.
Certified Quality Technician (CQT)
Organizations require Certified Quality Technicians (CQT) to ensure products consistently meet quality standards, reducing defects and improving customer satisfaction. CQT certification validates the technician's ability to interpret and utilize quality-related data effectively, leading to more informed decision-making. Certified technicians contribute to process improvements, resulting in greater operational efficiency and cost savings. They help maintain compliance with industry regulations, minimizing the risk of legal issues and enhancing brand reputation.
ISO 9001:2015 Lead Auditor Certification
Earning the ISO 9001:2015 Lead Auditor Certification equips a Quality Technician with a deeper understanding of quality management principles. With the certification, technicians can effectively assess and enhance an organization's quality management system, driving better consistency and customer satisfaction. The credential demonstrates a commitment to internationally recognized quality standards, increasing a technician's value within a competitive job market. It also provides the skills necessary to identify non-conformities and areas for improvement, ultimately leading to more efficient processes.
Lean Six Sigma Yellow Belt Certification
Obtaining a Lean Six Sigma Yellow Belt Certification provides a quality technician with foundational knowledge in process improvement methodologies. This credential equips them to identify inefficiencies within operational processes, directly resulting in higher quality outcomes. With this certification, technicians demonstrate their ability to support and participate in team-based problem-solving projects essential for maintaining competitive business practices. It also enhances their understanding of data-driven decision-making, which is crucial for ensuring product and service standards are consistently met.
Lean Six Sigma Green Belt Certification
Lean Six Sigma Green Belt Certification equips a Quality Technician with the skills to efficiently analyze and improve processes, leading to reduced defects and enhanced quality. Possessing this certification often results in improved problem-solving capabilities, which directly contributes to more efficient operations. Employers recognize the certification as a mark of expertise, increasing job prospects and potential salary growth. Companies benefit by experiencing significant cost savings and operational improvements through the application of these methodologies by certified technicians.
Certified Quality Inspector (CQI)
A Certified Quality Inspector ensures adherence to quality standards, impacting production consistency and customer satisfaction. Quality Technicians with CQI certification can accurately interpret blueprints and specifications, leading to fewer errors in the production process. The certification equips technicians with the tools to effectively use measurement and test instruments, verifying compliance with industry regulations. Enhanced problem-solving skills through CQI training result in quicker resolution of quality issues, improving overall operational efficiency.
Certified Quality Improvement Associate (CQIA)
Quality Technicians often encounter complex processes and systems, and CQIA certification deepens their understanding of quality improvement tools and methodologies, leading to enhanced performance. Effective problem-solving skills are crucial in this role, and CQIA provides a structured approach to identifying, analyzing, and resolving quality issues. The certification aligns with industry standards and practices, elevating a technician's competency and credibility in quality management. Organizations benefit from having CQIA-certified professionals as they contribute to continuous improvement initiatives, reducing errors and boosting overall productivity.
Statistical Process Control (SPC) Certification
Quality Technicians need Statistical Process Control (SPC) Certification to effectively monitor and control manufacturing processes, ensuring product consistency and reducing variability. Without this certification, technicians may struggle to identify and correct process anomalies, which could lead to increased defects and customer dissatisfaction. SPC Certification provides the necessary skills to implement data-driven decision-making, improving operational efficiency. Employers value certified technicians as they contribute to maintaining high-quality standards and minimizing waste, fostering a more efficient production environment.
Root Cause Analysis (RCA) Certification
A Root Cause Analysis (RCA) Certification equips quality technicians with the necessary skills to identify and address underlying issues, leading to more effective problem-solving. By mastering RCA methods, technicians can enhance process efficiency and reduce the recurrence of defects, which improves overall product quality. RCA certification also provides a standardized approach to diagnosis, ensuring consistency in quality assessments across the organization. An RCA-certified technician gains a competitive edge in the job market, as employers value the ability to prevent issues proactively.
Total Quality Management (TQM) Certification
Achieving a Total Quality Management (TQM) certification equips a quality technician with standardized methodologies and tools, enhancing process efficiency. Certification ensures a thorough understanding of quality principles, which leads to improved product consistency and customer satisfaction. Employers often require this certification as it signifies a technician's commitment to quality assurance and continuous improvement. The knowledge gained through TQM certification also enables technicians to effectively identify, analyze, and solve quality-related issues, thus reducing waste and operational costs.
Continuous Improvement Professional (CIP) Certification
The Continuous Improvement Professional (CIP) Certification equips a Quality Technician with advanced skills in process optimization, enhancing efficiency and effectiveness. It provides a structured framework for identifying and addressing inefficiencies, leading to better product quality and reduced costs. By mastering CIP principles, Quality Technicians can contribute to a culture of continuous learning and improvement within their organizations. Certification also differentiates technicians in a competitive job market, signaling a commitment to professional development and excellence.
Summary
When you acquire certifications as a Quality Technician, your competence in quality assurance processes can be significantly enhanced. This often leads to increased recognition and trust from employers, potentially resulting in career advancement opportunities. With certified skills, you help improve product or service quality, leading to higher customer satisfaction. Certification may also open doors to higher salary brackets due to the specialized expertise you bring to the table.